1. Equipment Overview
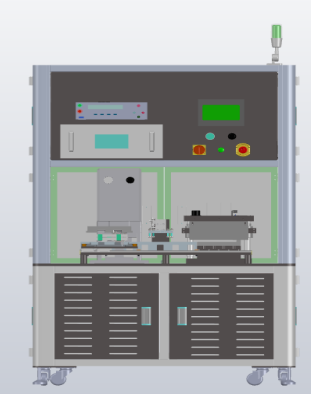
This equipment is used for pre-welding electrode tabs of cylindrical battery cells after winding/stacking, cutting the tabs, and testing for short circuits.
2. Equipment Process Flowchart
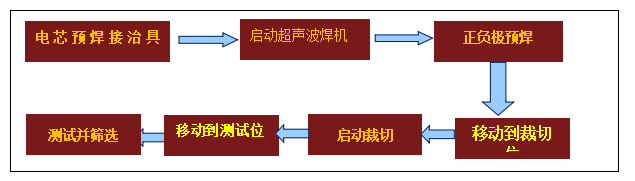
3. Technical Specifications
3.1 Equipment Dimensions
Length (L) | Width (W) | Height (H) |
---|
1200mm | 1000mm | 2200mm |
3.2 Ultrasonic Pre-welding
Specifications:
No. | Name | Parameter |
---|
1 | Substrate (Positive/Negative Electrode Foil) Material | Aluminum foil, copper foil |
2 | Substrate (Positive/Negative Electrode Foil) Thickness | 0.006-0.020mm |
3 | Shim (Positive/Negative Electrode Tab) Material | Aluminum tab, nickel tab, copper-plated nickel tab |
4 | Shim (Positive/Negative Electrode Tab) Thickness | 0.1-0.3mm |
5 | Maximum Number of Layers | 10-120 layers |
6 | Electrode Tab Welding Method | Horizontal/Vertical, to be determined before ordering |
7 | Weld Length | 33mm |
8 | Weld Width | 3mm |
9 | Weld Depth | 0.1-0.6mm |
10 | Welding Time | Within 1 second |
11 | Number of Rows of Weld Points | 2 rows |
12 | Pressure | 0.1MPa~1MPa, adjustable |
13 | Time Adjustment Range | 0.2~0.8/s, adjustable up to 60 seconds |
14 | Welding Surface Life | ≥100,000 times |
15 | Welding Head Material | Imported high-speed steel |
16 | Weld Point Height | 1mm |
17 | Weld Point/Pattern Distribution Status | Upper welding head straight pattern or V-pattern; lower mold mesh pattern |
18 | Distance from Welding Surface to Welding Head | >5mm |
19 | Length of Welding Head | ≤35mm |
20 | Available Welding Surface per Welding Head | 2 surfaces |
21 | Size of Individual Weld Point | 1mm x 1mm |
22 | Installation Direction of Welding Head | Horizontal |
23 | Adjustable Amplitude Range | Semi-cycle 20-40um |
24 | Frequency Difference between Transducers | ≤400Hz |
25 | Impedance Difference between Transducers | ≤4Ω |
26 | Capacitance Difference between Transducers | ≤400PF |
27 | Insulation Resistance between Transducer and Shell | ≥30MΩ |
28 | Power Tolerance | 8000W+ (peak) |
29 | Welding Tensile Strength | ≥300N |
30 | Frequency Control Method | Built-in adjustable frequency |
31 | Constant Amplitude Function | Switching power supply constant voltage constant current (constant amplitude) |
32 | Stepless Amplitude Adjustment | Stepless adjustment |
33 | Ultrasonic Frequency | 20KHz |
34 | Appearance | No virtual welding, weld penetration, missed joints; firm welding, layered penetration |
35 | Design Service Life of Equipment | 8-10 years |
36 | Weight | Approximately 60kg |
37 | Generator Size | Approximately 520×410×170mm (L×W×H) |
38 | Head Size | Approximately 480×200×480mm (L×W×H) |
39 | Efficiency | 8000W |
3.4 Cutting Section Components
No. | Name | Parameter |
---|
1 | Cylinder | Yadake |
2 | Cutter | SKD11 |
3 | Guide Post | Mold guide post |
4 | Safety Protection | Transparent acrylic |
3.5 Yangzi Short Circuit Tester
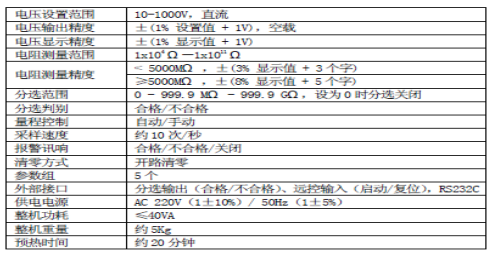
4. Main Components of Equipment
No. | Unit Name | Quantity | Notes |
---|
1 | Ultrasonic Welding Machine | 1 set | 6000W |
2 | Cutter | 1 set | Effective length 160mm |
3 | Tester | 1 unit | Digital display screen Yangzi |
4 | Mobile Platform | 1 set | Slide + platform |
5 | Electrical Control Unit | 1 set | Yenke |
6 | Frame | 1 set | Fangtong + aluminum profile |
Ultrasonic Pre-welder
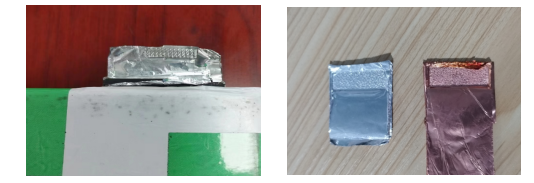
Pre-weld multiple layers of positive and negative electrode tabs of wound battery cells together.
Cutter
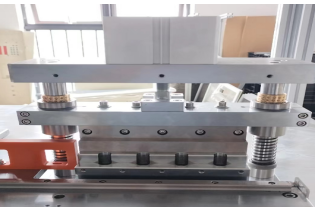
The cutter is made of SDK11 material, heat-treated, straightened, with a precision ground flatness of ±0.005mm.
Short Circuit Tester
The tester measures the insulation resistance of the positive and negative electrode tabs of the battery cell to ensure it meets process requirements.
5. Major Component Brands and Spare Parts List
Major Component Brands
No. | Name | Brand | Remarks |
---|
1 | PLC (CPU) | Panasonic / Xinje | Japan / Domestic |
2 | Touch Screen | Weintek / Xinje | China |
3 | Pneumatic Components | AIRTAC | China |
4 | Low-voltage Electricals | Chint | China |
5 | AC Contactors | Chint | China |
6 | Ultrasonic | Yenke | China |
7 | Cutter | Custom | China |
8 | Tester | Yangzi | China |
Note: Equivalent brands will be used if special circumstances arise.
Spare Parts List
No. | Name | Specifications | Quantity | Remarks |
---|
1 | Sensor | 1 piece/unit | Yadake |
|
2 | Jigs & Fixtures | 2 pieces | Domestic | Customized |
6. Random Tools List
No. | Name | Specifications | Quantity | Remarks |
---|
1 | Hexagon Wrench | 1.5-10 | 1 set |
|
2 | Open-end Wrench | 8mm-10mm | 1 piece |
|
3 | Open-end Wrench | 10mm-12mm | 1 piece |
|
4 | Ratchet Wrench | 250mm | 1 piece |
|
5 | Cross Screwdriver | 6*150mm | 1 piece |
|
6 | Toolbox | ZS-430 double layer | 1 piece |
|
7. Equipment Infrastructure Requirements
No. | Item | Content |
---|
1 | Dimensions | Equipment approximately 1200mm (L) x 1000mm (W) x 2200mm (H) (excluding operating space) |
2 | Power Requirements | Single-phase AC 220V±10%, 50Hz, earth line: protective grounding;Equipment installation power: 1.5KW, main power supply quantity: 1 |
3 | Compressed Air | Compressed air pressure: ≥0.6MPa, pressure fluctuation ±1% (clean air after water, oil, filtration, and stabilization);Compressed air consumption: 10m³/h, interface quantity: 1/unit;Interface air pipe specifications: Φ10mm |
4 | Environmental Requirements | Ambient temperature: Coating section 25±5℃ (according to buyer's process requirements);Relative humidity: 10%~30%RCH (according to buyer's process requirements);Cleanliness: Class 100,000 (according to buyer's process requirements) |
5 | Ground Requirements | Equipment total weight: approximately 0.4 tons;Cement or terrazzo floor, flatness ±5mm/㎡, bearing capacity ≥350kg/㎡. |