Equipment Function
This equipment is primarily used for the formation of hard-shell lithium-ion batteries under high-temperature (30–80°C) and negative-pressure (-10 to -75 kPa) conditions. It can rapidly activate battery formation performance at high temperatures, vacuum-extract air generated during battery formation, and simultaneously shorten the formation time, thereby reducing the battery manufacturing cycle.
Equipment Composition
The equipment consists of:
1 set of formation power supply cabinet (5V 60A, 32 channels).
1 set of pin-bed fixture group (32 channels per set).
1 set of negative-pressure vacuum system (1 layer, with 2 pipes of 20mm diameter per layer, divided into 16 points; each branch pipe has a diameter of 6mm, equipped with fluororubber anti-corrosion suction cups).
(Note: The power supply and fixture group are placed separately.)
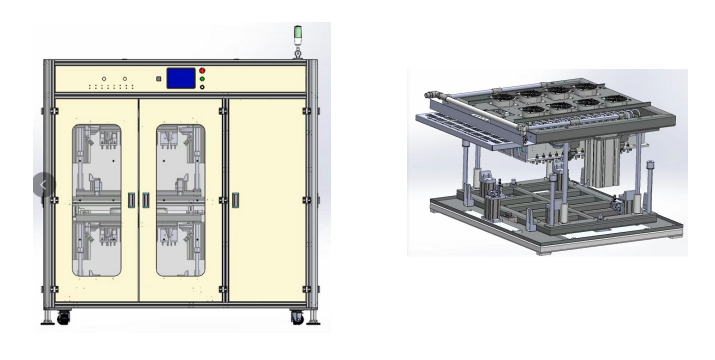
Rail lift vehicle delivers the fixture group → Push the fixture group into the pin bed → Activate the pin bed → Initiate the negative pressure process and start charging & formation → Formation completed → Automatically open the pin bed fixtures → Manually withdraw the fixture group via the rail lift vehicle → Next round of fixture group charging & formation
Applicable Aluminum Square Battery Dimensions: 72173204 (compatible range: thickness 38–75mm, width 120–180mm, height 110–220mm; adjustable based on actual needs).
Charge Voltage Setting Range: DC 0–5V
Discharge Voltage Setting Range: DC 5–2V (lower discharge limit is adjustable).
Charge/Discharge Current Setting Range: DC 0.05–60A
Voltage Accuracy: ±(0.05%RD + 0.05%FS)
Current Accuracy: ±(0.05%RD + 0.05%FS)
Voltage Resolution: 1mV
Voltage Stability: ≤0.1%
Current Resolution: 1mA
Current Stability: ≤0.1%
Charge Energy Efficiency: Up to 80%
Discharge Feedback Efficiency: Up to 78%
Power Accuracy: ±(0.05%RD + 0.05%FS)
Current Response Time: Hardware response time ≤50ms at 60A output.
Time Setting Range: Arbitrary setting within 0–9999 minutes; time units (h, min, s) selectable; resolution 0.1s.
Time Accuracy: ≤±0.1%
Recording Modes: Charge time, discharge time, rest time, and global recording time.
Recording Frequency: 100ms–65535s
Sampling Frequency: Approximately 10ms per cabinet.
Charging Modes: Constant current with voltage limit; constant current & constant voltage; constant power charging.
Charging Cutoff Conditions: Voltage; current; time; capacity; temperature.
Discharging Modes: Constant current discharge; constant power discharge.
Discharging Cutoff Conditions: Voltage; current; time; capacity; temperature.
Number of Steps per Cycle: ≤100 steps, with nested cycle function.
Continuous Operating Time: Equipment power must support full load operation of all channels, 24/7/365 uninterrupted.
Software Functions:
Supports various resumption modes: manual pause resumption, software shutdown resumption, power outage resumption, equipment communication interruption resumption, and abnormal stop resumption.
Supports barcode scanning (1D and 2D codes), with scanning modes including sequential scanning, channel skipping scanning, and tray loading scanning.
Stores detailed local test data; allows real-time viewing of current and historical data for each channel, presented in both data and curve formats. Supports exporting Excel reports individually or in batches, and can be set to export data automatically after test completion.
Supports capacity grading for battery classification.
Supports pass/fail judgment after test completion, based on specified cycle capacity, voltage, time, etc.
Supports step-specific protection and global protection against abnormal voltage, current, and temperature, with abnormal alarm functions.
Supports channel parallel connection (optional based on equipment).
Supports unit conversion.
Supports background database server storage or MES integration.
Software offline protection.
Free software upgrades provided.
Protection Functions:
Data anomaly recovery.
Software protection against overvoltage, undervoltage, overcurrent, undercurrent, and overcapacity.
Voltage and current protection thresholds configurable; alarms and records generated after protection activation.
Equipped with high-position alarm lights for status indication.
Emergency stop button installed; fixtures automatically open upon emergency stop.
Smoke alarm installed; equipment stops operation and triggers alarm when smoke is detected.
After equipment shutdown due to alarm, the process can resume from the interruption point without restarting from the beginning.
If communication between lower computer and upper computer is interrupted, normal operation resumes according to the original process after communication recovery.
Process steps can continue after unexpected power outage.
In case of communication interruption or PC failure, the equipment automatically enters a waiting state and resumes the current process after communication reset.
Vacuum System Parameters:
Achievable Vacuum Degree: -1kPa to -75kPa (equipment includes built-in vacuum pump and filtration buffer system).
Vacuum Setting Resolution: ±1kPa
Main Component Configuration
No. | Component Name | Brand |
---|
1 | Digital Vacuum Pressure Gauge | SMC |
2 | Pneumatic Components | Airtac/SMC |
3 | Temperature Controller | Omron/Panasonic |
4 | Test Probes | Custom (Gold-plated Copper) |
5 | Suction Cups | Custom |
6 | PLC | Mitsubishi/Xinje |
7 | Vacuum Pump | Custom (-90kPa, with Filtration Buffer) |
Random Accessories
No. | Component Name | Specification | Quantity | Service Life |
---|
1 | Test Probes | Custom | 5 pieces | >10,000 cycles |
Other Configuration Requirements
3.1 Includes power supply cabinet, one set of vacuum pump with (negative pressure anti-corrosion filter and buffer tank).
3.2 One stacker crane (capable of serving 10 machines), with one set of hot air heating system (customized).
3.3 One set of spare pallets for every 5 machines (10 on equipment, 2 spares; 16 positions per pallet, drawer-combined type).